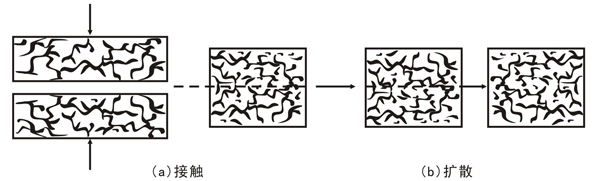
图8-14 胶料自黏过程
所谓自黏性,是指同种胶料两表面之间黏合性能。通常制品成型操作中多半是将同一类的胶片或部件黏合在一起,因此自黏性对半成品的成型如制品性能有重要作用。
自黏是黏合的一种特殊形式,大分子的界面扩散,对胶料的自黏性起着决定性的作用。扩散过程的热力学先决条件是接触物质的相容性;动力学的先决条件是接触物质具有足够的活动性。图8-14是胶料的自黏过程。
(1)接触 在外力作用下,使两个接触面压合在一起,通过一个流动过程,接触表面形成宏观结合。
(2)扩散 由于橡胶分子链的热运动,在胶料中产生微空隙空间,分子链链端或链段的小部分就能逐渐扩散进去。由于链端的扩散,导致在接触区和整体之间发生微观调节作用。活动性分子链端在界面间的扩散,导致黏合力随接触时间延长而增大。这种扩散最后造成接触区界面完全消失。
从上述自黏过程可以看出,橡胶分子的扩散需在一定的压力下进行,胶料的初始自黏强度随接触压力增大而增加;另外,橡胶分子的扩散过程也需要经历一段时间方能完成,因此胶料的自黏强度随接触时间增加而增大,自黏强度与接触时间的平方根呈线性关系。
一.橡胶分子结构的影响
(1)分子链柔性的影响一般说来,链段的活动能力越大,扩散越容易进行,自黏强度越大。例如顺丁橡胶,随1,2-结构含量增加,自黏强度明显增大。
因为1,2-结构中的乙烯基侧链上的双键比较容易围绕—CC一单键旋转而取向,而这种取向可增强两接触面之间的相互作用,所以随1,2-结构含量增加,接触面上的乙烯基数量也增加,于是提高了初始黏合强度。在最终自黏强度区域,试样的断裂属于内聚破坏,不发生在原来的界面上。试样的内聚破坏是聚合物分子链滑动的结果,而不是化学键断裂的结果。乙烯基侧链可能给分子链的滑动造成困难,所以增加1,2结构的含量,即增加乙烯基含量,会导致最终自黏强度提高,但所需的接触时间要长一些当分子链上有庞大侧基时,阻碍分子热运动,因此其分子扩散过程缓慢。
(2)分子极性的影响
极性橡胶其分子间的吸引能量密度(内聚力)大,分子难以扩散,分子链段的运动和生成空隙都比较困难,若使其扩散需要更多的能量。在丁腈橡胶胶料自黏试验中发现,随氰基含量增加,其扩散活化能也增加。
(3)不饱和度的影响
含有双键的不饱和橡胶比饱和橡胶更容易扩散。这是因为双键的作用使分子链柔性好,链节易于运动,有利于扩散进行。如将不饱和聚合物氢化使之接近饱和,则其扩散系数只有不饱和高聚物的47%~61%。
(4)结晶的影响
两种乙丙橡胶的自黏性试验表明,结晶性好的乙丙橡胶缺乏自黏性,而无定形无规共聚的乙丙橡胶却显示出良好的自黏性。因为在结晶性的乙丙橡胶中,有大量的链段位于结晶区内,因而失去活动性,在接触表面存在结晶区、链段的扩散难以进行。同样,在氯丁橡胶中有部分结晶时,自黏性下降;高度结晶时,自能性就完全丧失了。为使高度结晶的橡胶具有一定的自黏性,必须设法提高分于活动性,为此可提高接触表面温度,使之超过结晶的熔融温度,或以适当的溶剂使接触表面溶剂化。
二.填充体系的影响
无机填料对胶料自黏性的影响,依其补强性质而变化,补强性好的,自黏性也好。各种无机填料填充的天然橡胶胶料的自黏性,依下列顺序递减:白炭黑>氧化镁>氧化锌>陶土。炭黑可以提高胶料的自黏性。在天然橡胶和顺丁橡胶胶料中,随炭黑用量增加,胶料的自黏强度提高,并出现最大值。填充高耐磨炭黑的天然橡胶胶料,随炭黑用量增加,自黏强度迅速提高,在80质量份时自黏强度最大;顺丁橡胶胶料在高耐磨炭黑用量为60质量份时,自黏强度最高。当炭黑用量超过一定限度时,橡胶分子链的接触面积太少,造成自黏强度下降。天然橡胶比顺丁橡胶的自黏强度高,是因为天然橡胶的生胶强度和结合橡胶数量都比顺丁橡胶高。
三.增塑剂的影响
增塑剂(或软化剂)虽然能降低胶料黏度,有利于橡胶分子扩散,但它对胶料有稀释作用,使胶料强度降低,结果使胶料的自黏力下降。
四.增黏剂的影响
使用增黏剂可以有效地提高胶料的自黏性。常用增黏剂有松香、松焦油、妥尔油、萜烯树脂、古马隆树脂、石油树脂和烷基酚醛树脂等,其中以烷基酚醛树脂的增黏效果最好。容易喷出的配合剂,如蜡类、促进剂TMTD、硫黄等应尽量少用,以免污染胶料表面,降低胶料的自黏性胶料焦烧后,自黏性急剧下降,因此对含有二硫代氨基甲酸盐类秋兰姆类等容易引起焦烧的硫化体系要严格控制,使其在自黏成型前不产生焦烧现象。