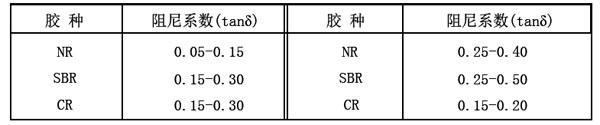
表1 几种橡胶的阻尼系数
硫化体系对减震橡胶的刚度、阻尼系数、耐热性、耐疲劳性均有较大的影响。一般在硫化胶的网络结构中,交联键中的硫原子及游离硫越少,交联越牢固,硫化胶的弹性模量越大,阻尼系数越小。使用传统硫化体系,并适当提高交联程度,对减震和耐动态疲劳性有利,但耐热性不够。例如天然橡胶采用有效硫化体系和半有效硫化体系时,虽然耐热性得到改善,但抗疲劳性能以及金属件的黏着性则有下降的趋势。因此,必需要使这些性能得到恰当的平衡。采用硫黄硫化体系所能达到的耐热性毕竟是有限的,因此对耐热等级更高的新型无硫硫化体系进行了研究。
某些耐热性较好的橡胶,如氟橡胶、丙烯酸酯橡胶、三元乙丙橡胶、硅橡胶、氢化丁腈橡胶、氯磺化聚乙烯、共聚氯醇橡胶,由于它们在高变形下的耐疲劳性能以及与金属粘接的可靠性都比较差,因而不宜用作减震橡胶。如果需要使用这些橡胶则必须克服上述缺陷,通过高变形下(实际使用条件考核)的试验鉴定后方可使用。
填充剂是除橡胶之外影响胶料动态阻尼特性最为显著的因素,它与硫化胶的阻尼系数和模量有密切关系。硫化胶在形变的情况下,橡胶分子运动时,橡胶链段与填料之间或填料与填料之间的内摩擦,会使硫化胶的阻尼增大。该增值与填料和橡胶的相互作用及界面尺寸有关。填料的粒径越小,比表面积越大,则与橡胶分子的接触表面增加,物理结合点较多,触变性较大,在动态应变中产生滞后损耗,而且粒子之间的摩擦也会因表面积增大而增大,因此表现出tanB较大,动、静态模量也较大。填料的活性愈大,则与橡胶分子的作用越大硫化胶的阻尼性和刚度也随之增加。填料粒子的形状对胶料的阻尼特性和模量也有影响,例如片状的云母粉可使硫化胶获得更高的阻尼和模量。
在减震橡胶的配方中,天然橡胶使用半补强炉黑和细粒子热裂炭黑较好。在合成橡胶中,可使用快压出炭黑和通用炭黑。一般随炭黑用量增加,硫化胶的阻尼和刚度也随之提高。在炭黑用量一定的情况下,粒径小、活性大的高耐磨炭黑的阻尼性和刚度均高于半补强炭黑。另外,随炭黑用量增加,对振幅的依赖性也随之增大。随振动振幅增加,炭黑用量越大,模量降低和阻尼增加越显著。在振幅很小(趋于0时),阻尼系数与填料含量关系不大。
综上可见,随炭黑粒径减小、活性增大、用量增加,减震橡胶的阻尼系数和模量也随之提高。但是从耐疲劳性来看,炭黑在减震橡胶中却有不良的影响:炭黑的粒径越小,则疲劳,作用越显著,疲劳破坏也越重。对于高阻尼隔震橡胶来说,在橡胶中加入炭黑等填充剂后,由于橡胶分子被炭黑粒子表面所吸附以及炭黑粒子间存在橡胶连续相和某些配合剂的不连续相,加上橡胶分子链本身的摩擦,使体系的表观黏度系数增大;且炭黑含量越高,黏度越大。若向橡胶、炭黑体系施加,应力时,橡胶分子链产生的滑移从原来的炭黑-橡胶表面脱离,然后再重新吸附并使炭黑凝聚相破坏,而后再凝聚,产生很大的摩擦能。
为了尽可能提高减震橡胶的阻尼特性,降低蠕变及性能对温度的依赖性,往往在高阻尼隔振橡胶中配合一些特殊的填充剂,例如蛭石、石墨等,在由橡胶和特殊填充剂构成的体系内引起内摩擦,将施加到体系内的部分机械能转化为热能而耗散掉,这便是高阻尼隔振橡胶的减震原理。
白炭黑粒径小,补强效果仅次于炭黑,但是动态性能远不如炭黑。碳酸钙、陶土、碳酸镁等无机填料,补强性能一般较弱。为了获得规定的弹性模量,其用量比炭黑大,这对其他性能会产生不利的影响,所以一般很少采用。用作减震橡胶的增塑剂,除了具有降低玻璃化温度Tg。和改善加工性能的作用外,还要求使阻尼转变区增宽,这种增宽作用主要取决于增塑剂的特性及其与橡胶的相互作用。如果增塑剂在橡胶中只有一定限度的溶解度,或增塑剂根本不相容而纯属机械混合,则阻尼转变通常在减震橡胶中,随增塑剂用量增加,硫化胶的弹性模量降低,阻尼系数tan增大区就会变宽在减震橡胶中添加增塑剂,虽然能改善橡胶的低温性能和耐疲劳性能,但同时也会使蠕变和应力松弛速度增加,影响减震橡胶的阻尼特性和使用可靠性,因此增塑剂的用量不宜过多。
一般增塑剂的分子结构与生胶的分子结构在极性上要匹配,即极性橡胶选用极性增塑剂,反之亦然。对于天然橡胶,通常使用松焦油、锭子油等增塑剂。对丁腈橡胶则以苯二甲二丁酯、癸二酸二辛酯、邻苯二甲酸二辛酯和己二酸二异辛酯等为主。
以上所述为个人观点(欧文新材料),仅供胶友参考,环保型橡胶助剂(硫化剂、促进剂、防老剂、活性剂等特种胶欢迎来电咨询)。