表3-1 常用橡胶的挤出温度范围
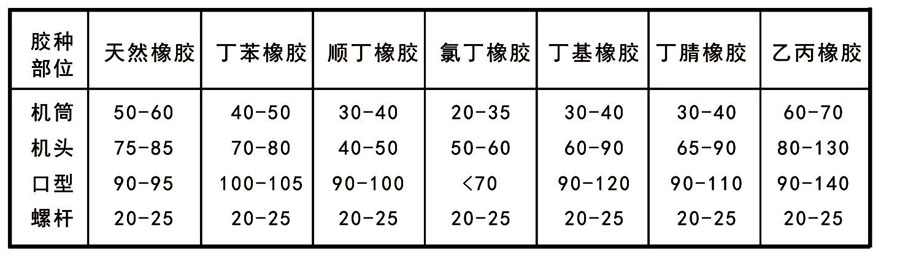
主要是温度、速度。合理控制温度,可保证挤出顺利进行,提高产量并改善挤出半成品的质量,如使半成品外表光滑、尺寸稳定,准确和膨胀率小。挤出温度过低会使半成品表面粗糙、断面增大、电负荷增大;挤出温度过高,则会引起胶料焦烧和起泡等。为此,挤出过程必须采用最佳温度分布。通常,挤出机不同部位应采用不同温度。一般情况是机筒最低,机头较高,口型最高;机筒又可以分作一个或多个温度控制区段,而螺杆温度则总是高于机筒。
加料段温度一般较低,有利于加料和改善压出均匀性。对大部分胶料来说,温度设定在43-60℃即可;对较硬的胶料,可适当提高温度,为49-60℃。
机头和口型温度较高有两个好处:一是可降低挤出半成品的膨胀率;二是可降低机头压力,有利于提高挤出产量。机筒温度较低可使胶料黏度增大。因此,在实际操作中,控制机筒温度低于螺杆温度有利于提高产量。但是,机筒与螺杆温度差必须控制在合理的范围内。温度差过大,虽能提高产量,但是会引起挤出半成品的质量下降,容易出现微孔和螺旋形等缺陷;温差太小,则会降低产量。
常用橡胶的挤出温度范围见表3-1。
挤出速率快,流量大,但半成品膨胀率和收缩率较大,表面粗糙,胶温高,容易发生焦烧。挤出速率低,半成品表面光滑,膨胀率和收缩率小,但产量减少。因此,必须权衡挤出半成品质量和产量的要求,正确调节和控制挤出速率。
挤出速率与胶料黏度有关,挤出流量随胶料黏度降低而增大,即挤出速率随黏度增大而降低。同时黏度随温度而变化,挤出温度升高,会引起黏度降低,因而也能使挤出速率增大和流量增加。
软化剂对挤出速率的影响表现为两种情况:凡士林、石蜡和硬脂酸等可加快挤出速率;黏性软化剂,如树脂和沥青等会减慢挤出速率。
补强填充剂对挤出速率的影响比较明显,添加填充剂能提高挤出速率,并减少挤出膨胀率和改善表面状态。添加软质炭黑胶料的挤出速率比添加硬质炭黑者为快,含炉法炭黑的挤出速率比槽法炭黑者为快。最适宜的填充剂为快压出炉黑、半补强炉黑、碳酸镁和陶土等。
在挤出温度和胶料配方确定条件下,控制挤出速率的关键是正确确定螺杆转速。为防止湍流,螺杆转速不能过快,在无旁压辊情况下,螺杆临界转速可按下式来确定:
挤出速率应根据所挤出制品的规格来确定,通常挤出速率为3-20m/min,螺杆转速宜控制在30-50r/min。选择这一参数的原因是,挤出胶料质量往往与胶料黏度变化或波动有关。在低剪切速率区内,胶料黏度随剪切速率变化较大。因此挤出速率低时,会引起挤出不稳定。螺杆转速在30r/min以上时,胶料黏度可渐趋平稳。
一般来说,冷喂料挤出机比热喂料挤出机的螺杆转速低;小型挤出机比大型挤出机的螺杆转速高;难挤出的胶料应比易挤出的胶料的螺杆转速低。